Table of Contents • changes in shipment volume; • changes in distribution channels; • excess and obsolete inventory and inventory holding charges; • expediting costs incurred to meet customer delivery requirements; • changes to the IRA; • tariffs assessed on our products imported to the U.S. and elsewhere; and • fluctuations in foreign currency exchange rates. Fluctuations in gross profit may adversely affect our ability to manage our business or achieve or maintain profitability. We are under continuous pressure to reduce the prices of our products, which has adversely affected, and may continue to adversely affect, our gross margins. The solar power industry has been characterized by declining product prices over time. We have reduced the prices of our products in the past, and we expect to continue to experience pricing pressure for our products in the future, including from our major customers. In addition, we have reduced our prices ahead of planned cost reductions of our products, which has adversely affected our gross margins. When seeking to maintain or increase their market share, our competitors may also reduce the prices of their products. In addition, our customers may have the ability or seek to internally develop and manufacture competing products at a lower cost than we would otherwise charge, which would add additional pressure on us to lower our selling prices. If we are unable to offset any future reductions in our ASPs by increasing our sales volume, reducing our costs and expenses or introducing new products, our gross margins would continue to be adversely affected. Given the general downward pressure on prices for our products driven by competitive pressure and technological change, a principal component of our business strategy is reducing the costs to manufacture our products to remain competitive. If our competitors are able to drive down their manufacturing costs faster than we can or increase the efficiency of their products, our products may become less competitive even when adjusted for efficiency, and we may be forced to sell our products at a price lower than our cost. Further, if raw materials costs and other third-party component costs were to increase, we may not meet our cost reduction targets. If we cannot effectively remain price competitive, this could result in lost market share and lower gross margins. If we do not forecast demand for our products accurately, we may experience product shortages, delays in product shipment or excess product inventory, any of which will adversely affect our business and financial condition. We manufacture our products according to our estimates of customer demand. This process requires us to make multiple forecasts and assumptions relating to the demand of our distributors, their end customers and general market conditions. Because we sell most of our products to distributors, who in turn sell to their end customers, we have limited visibility as to end-customer demand. We depend significantly on our distributors to provide us visibility into their end-customer demand, and we use these forecasts to make our own forecasts and planning decisions. If the information from our distributors turns out to be incorrect, then our own forecasts may also be inaccurate. Furthermore, we do not have long-term purchase commitments from our distributors, installers or end customers, and our sales are generally made by purchase orders that may be canceled, changed or deferred without notice to us or penalty. As a result, it is difficult to forecast future customer demand to plan our operations. If we overestimate demand for our products, or if purchase orders are canceled or shipments are delayed, we may have excess inventory that we cannot sell. We may have to make significant provisions for inventory write- downs based on events that are currently not known, and such provisions or any adjustments to such provisions could be material. We may also become involved in disputes with our suppliers who may claim that we failed to fulfill forecast or minimum purchase requirements. Conversely, if we underestimate demand, we may not have sufficient inventory to meet end-customer demand, and we may lose market share, damage relationships with our distributors and end customers and forgo potential revenue opportunities. Obtaining additional supply in the face of product shortages may be costly or impossible, particularly in light of supply chain disruptions and our outsourced manufacturing processes, which could prevent us from fulfilling orders in a timely and cost-efficient manner or at all. In addition, if we overestimate our production requirements, our contract manufacturers may purchase excess components and build excess inventory. If our contract manufacturers, at our request, purchase excess components Enphase Energy, Inc. | 2023 Form 10-K | 35
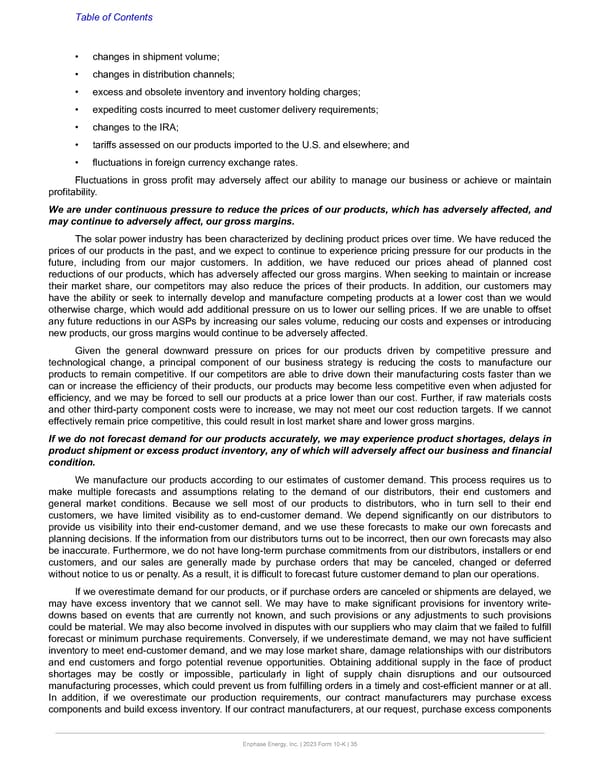